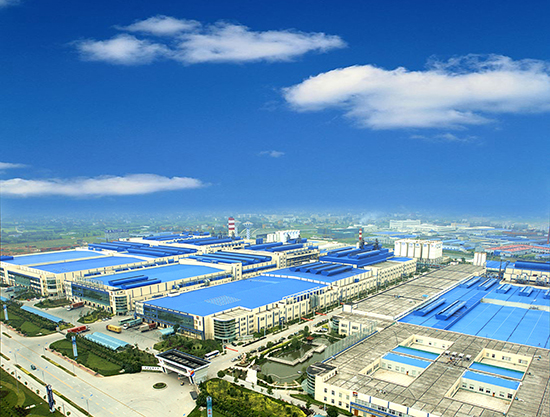
巨石60万吨玻纤工业基地
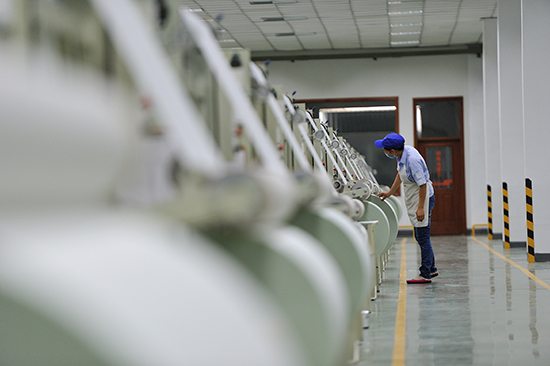
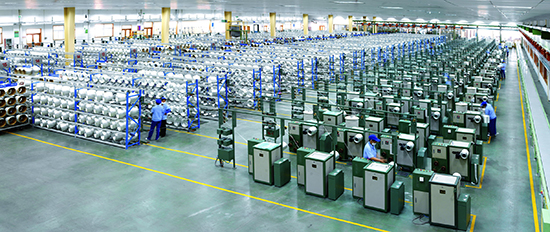
工厂生产车间
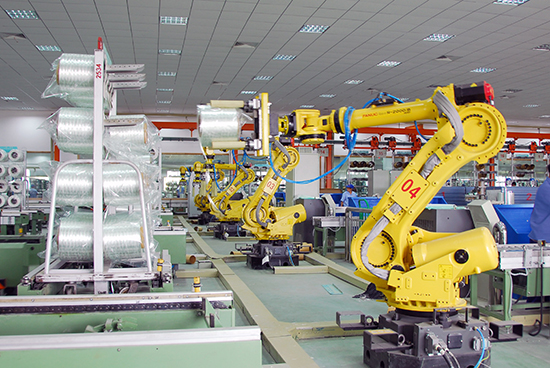
检装车间机械手
编者按:随着中国经济迈入新常态,作为中国市场经济最发达地区之一的浙江,工业经济较早进入新常态,既让浙江经受了严峻的考验,也锻炼提高了浙江应对新常态的能力,有信心在新常态下重塑浙江工业发展新优势。新常态下,推进经济发展、转型升级,动力转换是关键,必须依靠改革开放和创新驱动这两大新动力。浙江以“四换三名”为总抓手——腾笼换鸟、机器换人、空间换地、电商换市,培育名企、名品、名家,做强实体经济,加快发展信息、环保、健康、旅游、时尚、金融、高端制造等七大产业。
?? ??一个储存能力85176个货位的仓储区,日常的操作员工只要4个,16台双伸位堆垛机、400余台地面输送设备和4套触摸式地面人机操作站,通过总控调度系统统一调度分配,实现了货物的自动化存取。
这正是巨石集团有限公司自动化仓储中心的立体仓储区,通过全面实施“机器换人”,目前已经实现仓库作业的机械化、自动化,大大的提高了工作效率,并解决储存品种受限的难题。
近两年,桐乡市把“机器换人”作为重要抓手,促进装备制造业加快发展,取得一定成效,为省内惟一连续两年(2013、2014)获省“机器换人”考核一等奖的县市,连续两年获省120万元和120亩土地的政策支持。
在桐乡,巨石集团也确立集团以管控一体化为核心、生产制造智能化、IT服务智慧化为基础的“一核两基”信息化建设体系,不断的自主创新,推进生产线装备提升和技术改造,在智能工厂的探索之路上越走越远。
鼓励创新 自制机器人改造生产线
巨石集团是全球最大的玻璃纤维专业制造商,作为世界玻纤的领军企业,多年来一直在规模、技术、市场、效益等方面处于领先地位。
“从整个玻纤行业来说,我们集团一直是引领整个行业的,没有什么借鉴的标杆,都是别人来借鉴我们。”巨石集团体系管理部副总经理于亚东在接受采访时表示,巨石的成功离不开不懈的探索和创新。
这一点在巨石生产线的装备提升改造上得到了很好的印证,由于玻纤产品和生产线的特殊性,许多引进的机器人并不能适应生产需要,巨石便专门成立项目“攻关小组”,用于改造和自制机器人。
记者在巨石集团三分厂的生产车间里看到,一个个重达15-20公斤的4个玻纤成品从生产流水线上完成自动贴标后,由竖着4组“手指”的机器人从传送带上搬下,等待下一步集装和仓储。
于亚东说:“这个机器人就是我们集团自主改造的,从最初的1组手指到现在的4组,经过反复的改良试验,目前已经比较成熟。”
于亚东表示,巨石每年在装备提升上的研发投入达到3000万-5000万。因此,自制的机器人在工厂车间里并不少见,“都是巨石员工经过反复摸索和试验改造出来的。”
如今,巨石集团上下已经形成了一套“由工人提出设想——技术人员转化成可行技术方案——制作成品进行小范围试验——展示成果全面推广”的创新模式。
此外,巨石集团还有一套鼓励创新的机制。每年年初时,集团在重点需要攻克领域,都会成立专门攻关的招标项目,在集团内部公开招标,投中方若在一年内做出成果突破并通过集团验收,将会得到重大奖励。
有了先进的创新模式和鼓励机制,巨石在生产线的改造提升成果显著。除了自动化的生产线外,车间里需要人工完成的工作已经基本都换成了机器,并且在不断完善。
生产智能化带动管理模式变革
巨石的自主创新精神使“机器换人”进展顺利,生产也不断步向智能化,而这也带动管理模式产生变革。
“国家在大力推进两化深度融合,集团领导也在转变观念,传统的管理和看报表的形式已经跟不上我们现在整个生产设施变化的需求,我们的高层迫切希望在办公室就能看到生产现场。”于亚东说。
如今,巨石集团大到总部统一控制的ERP系统(这是一个业务统一、操作权限统一、管理流程统一制订的综合业务和信息门户,在办公室里就能实现了从生产到物流的一体化管控),小到每道工序的自动化控制系统(实现了24小时监控,有专业的人员进行跟踪,及时对异常情况进行反馈处理),都实现了信息化系统的实时自动管理,提高了一线工作的舒适性和安全性。
“机器换人”换来巨大经济效益
据了解,巨石集团每年都会按计划,对1-2条生产线进行装备提升和技术改造。经过数年的改进,巨石2014年单个生产线相比2008年能耗下降25%,生产效率提升10%,预计2015年能耗降低突破30%,效益提升到达到12%-13%。
随着信息化系统的上线运行,巨石集团各业务单位工作准确率在原有基础上得以有效提高,数据准确率在99.9%以上,工作质量和数量得到有效提升,“机器换人”换来了巨大的经济效益。
“2008年的时候,我们集团员工总数10800人,通过“机器换人”,现在精简到8000人,如果人均按8W来算,节省下来的人工成本要以亿来计算。”于亚东说。
另外,信息化系统也使巨石水、电、气等能源也得到实时监控,使用量得以有效控制,为国家节能减排做出了贡献。
去年,桐乡市出台了《桐乡市“机器换人”奖励(补助)实施细则》,对纳入市工业生产性投资奖励的项目,从高执行工业投资项目奖励标准;对未纳入市工业生产性投资奖励的项目、自主研发或自制设备项目,按实际设备或相关投资额分行业给予3-6%的奖励。对成效突出的示范企业及优秀服务机构给予一次性奖励(补助)5万元。同时还组织指导企业申请省级资金。巨石的项目成功入围省百项示范工程,还被列入信息化和工业化融合管理体系贯标试点企业,获得了不菲的奖励。
智能工厂项目已经扬帆
“现在,巨石集团在‘机器换人’和管理软件上都达到了一定程度,那么生产和管理应该怎么衔接成为首要矛盾,打造智能车间也就自然的被提出来。”于亚东表示。
据了解,如今玻纤的自动化生产线已经具备了数据采集的条件,管理软件也很完整,智能工厂的改造有了技术保障和硬件设备支撑,智慧工厂项目成为巨石集团今年的重点规划项目。
于亚东透露:“该项目马上要进入招标阶段,集团预计用2-3年时间完成桐乡基地的智慧改造。”
对于实行“机器换人”推进两化融合的原因,于亚东认为这既是集团的战略引领,同时也是需求导向。
(审核编辑: 智汇小蟹)